STRENGTH OF YAMATOYAMATOの強み
01一括受注設計から、加工、組立、納品まで
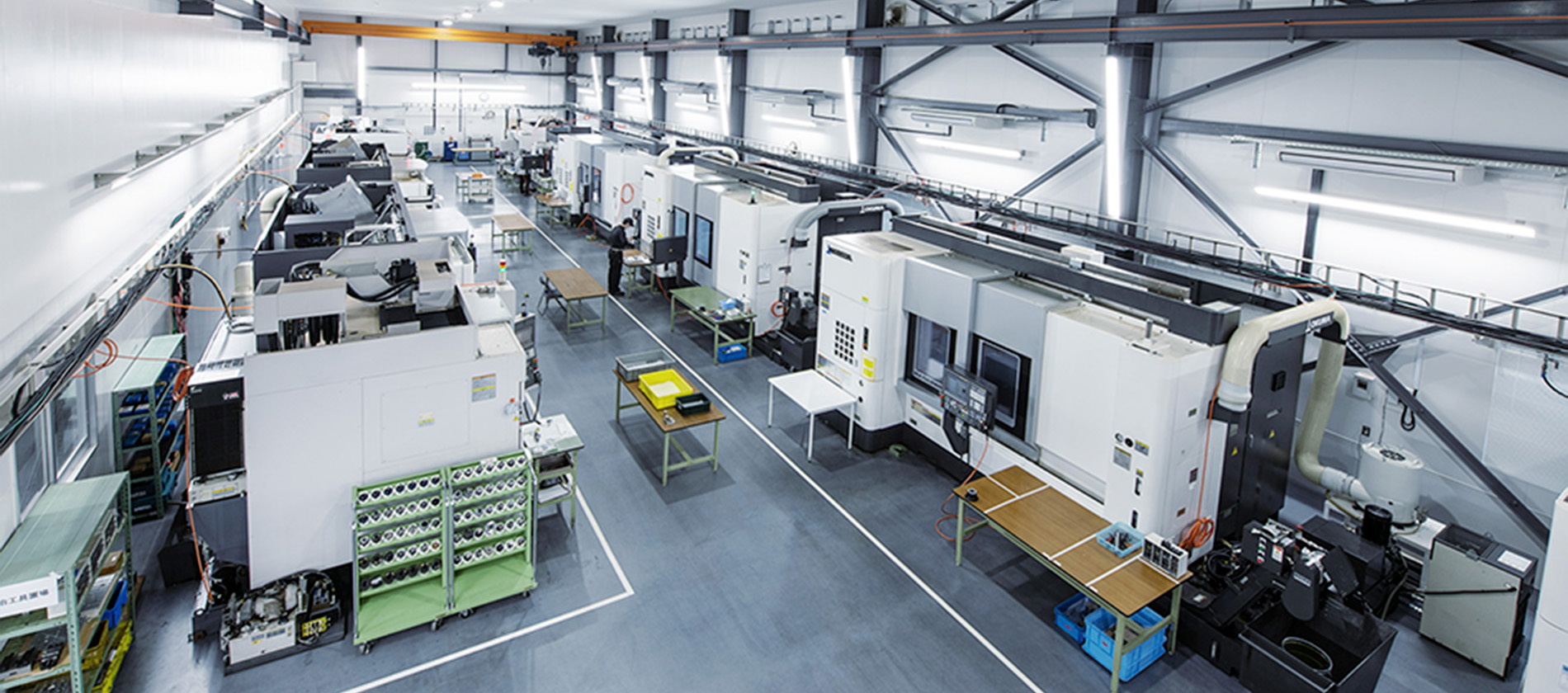
ADVANTAGES一括受注のメリット
-
メリット1
納期短縮、納期管理、品質管理やバックオフィス業務の手間が大幅に減る
-
メリット2
コスト削減を実現
-
メリット3
設計も制御プログラムも
OK
発注や納品管理の手間を大幅に軽減
和コーポレーションの強みのひとつである「一括受注」。切削や板金などの加工、機械の組立をはじめ、設計から機械制御のプログラム、納品まで一括で受注しています。
板金と切削部品の溶接、その後の再加工や洗浄、再検査など、本来であれば複数の業者に依頼するような加工や処理を一括発注できるので、管理の手間を大幅に減らすことが可能です。また、ひとつの企業の中でほぼすべての工程を行うことで、コストやスピードに関してもメリットが生まれます。
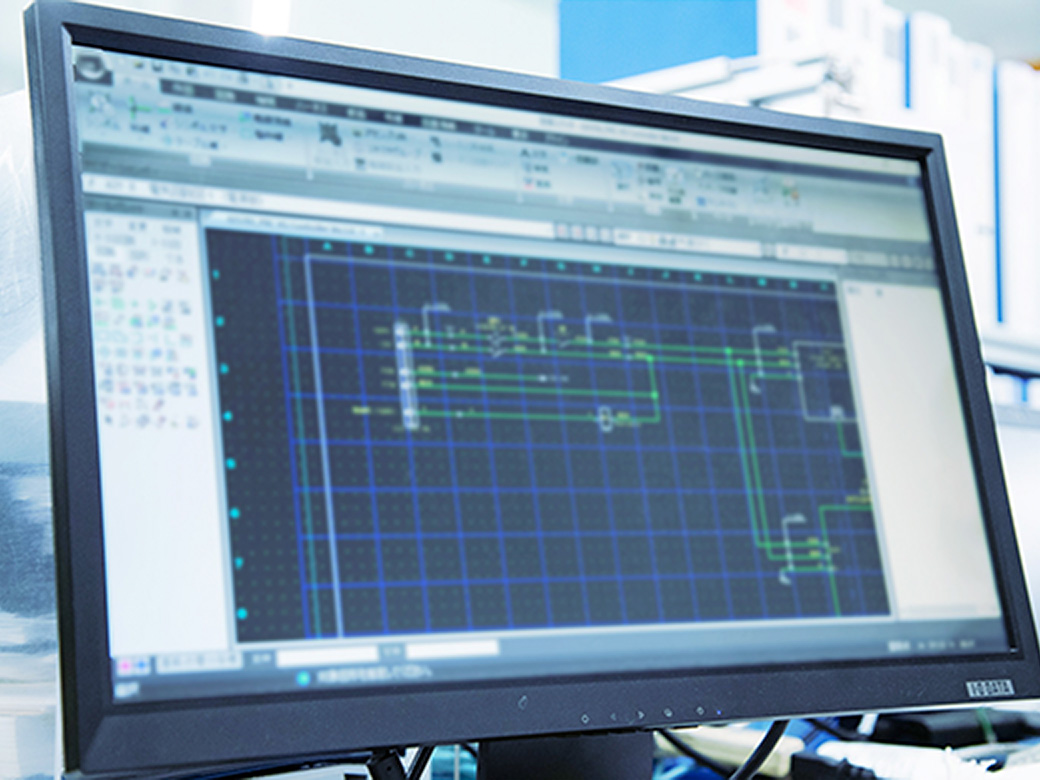
得意なのは仕様やサイズが変わる製品
例えば、ロットごとにサイズや仕様が変わる製品の生産にお悩みであれば、ぜひ和コーポレーションにご相談ください。大まかな仕様をお伝えいただくだけで、機械設計、機械制御、バリューエンジニアリングのご提案、加工、組立、納品までの流れを一括でお任せいただけます。
多数の大型製品の組み立てやクリーンブース環境下での装置組み立てにも対応。治具の設計からヘリウムリークディテクターの検査、既存の装置の改造、ポンチ絵のアイディアからの装置構想、PLCの選定から、シーケンサーのプログラム、タッチパネルのデザイン設計まで、幅広く対応いたします。
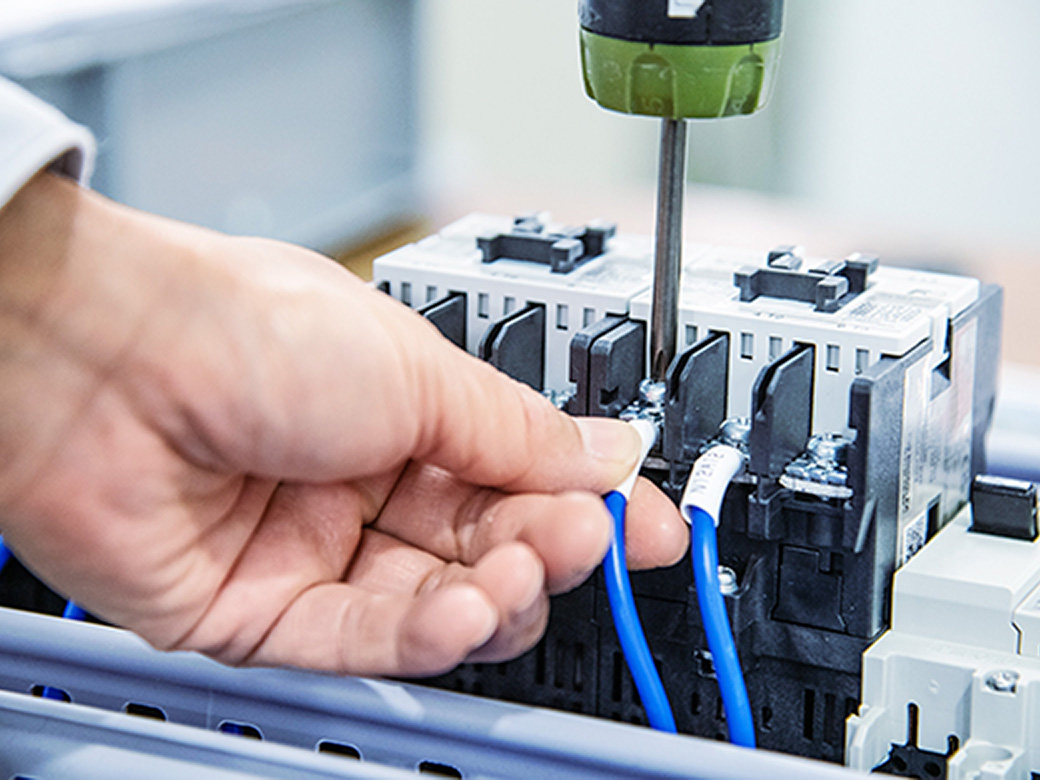
WORK FLOW一括受注の流れ
-
1
設計・プログラミング・VE 加工や組立の知識をもった開発者・設計者が複数在籍。量産を前提とした効率的な機械設計が可能です。すでに設計図がある場合でも、量産に合わせた設計図のチェックや修正のご提案も可能。量産に入る前段階から安心してご依頼いただけます。また、機械装置制御のプログラミングについてもお任せいただけます。
-
2
部品加工、フレーム加工
■高精度の切削、旋盤
保有設備(マシニングセンタ) 保有設備(複合加工機) 保有設備(旋盤・その他)
5軸制御のマシニングセンタ、インテリジェント複合加工機など、難削材や大型の加工に対応した多彩な設備を保有しています。■精密板金、溶接
保有設備(Laser&Welding(精密板金))
高精度な寸法を求められる板金に対応した曲げ加工機やロボット溶接機、電子ビーム溶接機を保有。チタンの溶接も可能です。 -
3
部品検査 部品の品質保証、測定データ管理、お客様納入品質の不具合・取引先(委託先)品質の不具合の是正を行っています。
保有設備(品質管理設備)
製作前後のチェックシートによる工程内保証を実施。万一不具合が出た場合も内部トレーサビリティが確立しているため、不具合の理由の報告、工程の改善などに迅速に対応できます。 -
4
組立 半導体製造装置、フラットパネル検査機、製造装置の冷却配管、搬送系(ベルトコンベア)、食品加工装置、自動車部品検査装置、家電製品向け量産装置などの組立を行っています。装置の組立から配線作業、ハーネス製造、真空装置向けの作業も得意です。
-
5
最終検査 自社調達、お客様支給部品を含め、お客様のご要望に応じた検査メニューに対応します。
ユニット単位や装置・機器、システムの完成後に、火入れのみ(電源)からシステムチェック、デバッグ、機能確認、マラソンラン、外観検査、VE、次回改善点の要望聞き入れまで、幅広く対応。お客様とチェックリストを作り対応したチェックも行っています。
中空構造体や溶接、真空部品のヘリウムリークディテクターによるリーク検査も実施出来ます。 -
6
梱包・配送 自社でトラックを多数所有。エアサス、ウイングタイプの4トン車も備えているため、精密機器の搬送も可能です。自社での配送が可能なことで、緊急時の材料の引き取りから納品のスケジュール調整にも柔軟に対応できます。
ほかのYAMATOの強みを見る